Table Of Contents:
- How to Maximize Energy Efficiency in Coffee Roasting: Power Consumption, Insulation, and Roasting ROI Explained
- What Are the Key Factors Affecting Roaster Power Consumption?
- What Are the Best Insulation Options for Coffee Roasters?
- How to Calculate Roasting ROI Based on Energy Efficiency Improvements?
- What Are Sustainable Roasting Practices That Enhance Energy Efficiency?
- How Can Energy Audits and Consulting Improve Roaster Efficiency and ROI?
- What Are the Latest Innovations in Energy-Efficient Coffee Roasting Equipment?
- How to Maintain and Monitor Roaster Energy Efficiency Over Time?
- Table: Comparison of Key Energy Efficiency Components in Coffee Roasters
- Frequently Asked Questions
- Final Thoughts
How to Maximize Energy Efficiency in Coffee Roasting: Power Consumption, Insulation, and Roasting ROI Explained
Coffee roasting is both an art and a science that demands precise energy management to produce high-quality roasted beans while keeping operating costs low. many coffee roasters invest in advanced techniques to optimize heat distribution and achieve consistent profiles. In this article, I share comprehensive insights into maximizing energy efficiency by examining power consumption factors, insulation options, roi calculations, sustainable practices, energy audits, and innovations in roasting equipment. these strategies help coffee roasters not only conserve energy but also boost profitability and support environmental sustainability.
What Are the Key Factors Affecting Roaster Power Consumption?
When analyzing power consumption, the roaster’s design is critical. The type, capacity, and mechanisms during the roast cycle determine energy needs. Understanding heat source efficiency and airflow management is essential for optimal energy use.
How Does Roaster Design Influence Energy Use?
Roaster design significantly impacts power consumption. Roasters with insulated chambers and efficient heat distribution can use up to 20% less energy than less optimized models. Features such as recirculating hot air systems and integrated temperature sensors help ensure energy is used only when needed. High thermal mass materials like cast iron and ceramics retain heat longer, reducing constant power input.
Which Roasting Machine Components Consume the Most Energy?
The most energy-intensive components include heating elements, fans, and afterburner systems. The heating element supplies the needed heat, while fans maintain uniform temperature profiles. The afterburner, which burns off chaff, can contribute significantly to energy use if not managed properly. Optimizing fan speed and using variable frequency drives (VFDs) can reduce energy use by 15%–25%.
How Can Energy-Saving Roasting Techniques Reduce Power Consumption?
Energy-saving roasting techniques combine technological adjustments with process improvements. Pre-heating strategies that use residual heat from previous batches lower the energy needed for new cycles. Automatic shutdown protocols and dynamic airflow adjustments—such as “duty cycling” the heating element based on sensor feedback—can result in savings of up to 10% on power bills.
What Are the Best Insulation Options for Coffee Roasters?
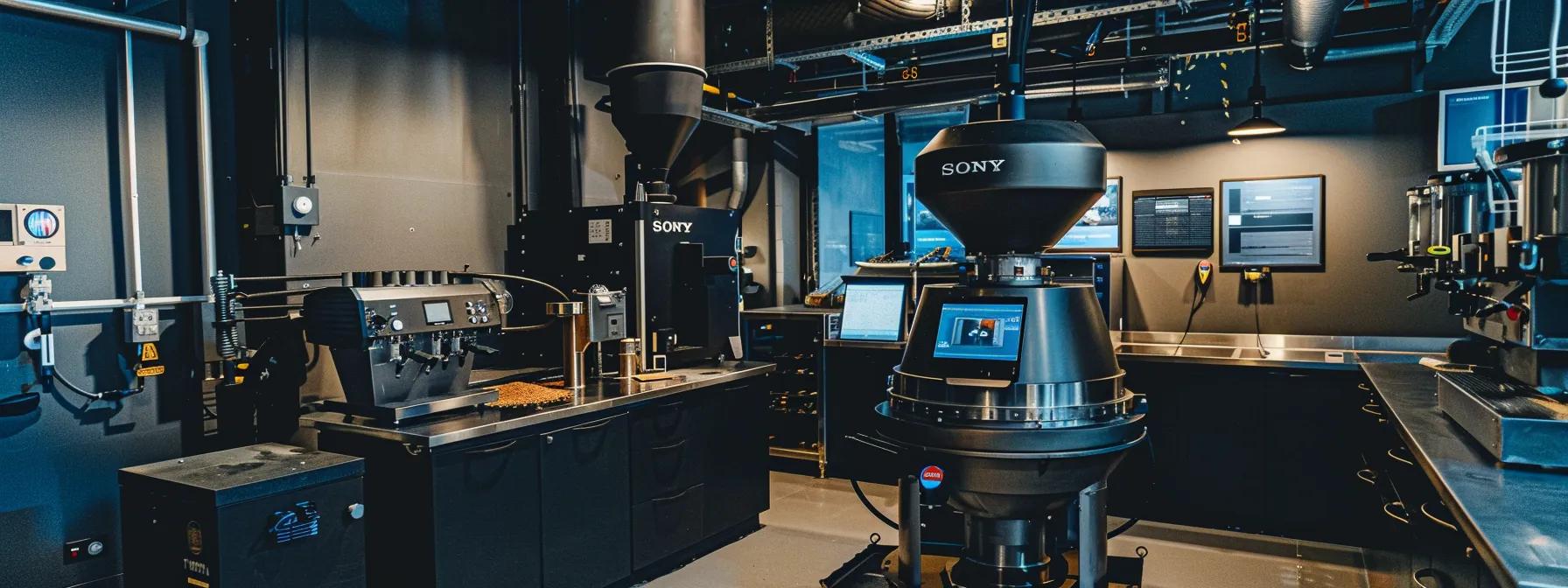
Insulation is key to reducing energy consumption by minimizing heat loss and maintaining stable roasting chamber temperatures. A well-insulated roaster delivers consistent roast quality and improves operational economics.
How Does Insulation Improve Roaster Energy Efficiency?
Effective insulation slows heat transfer from the hot chamber to the cooler surroundings, reducing the need for extra heating. Roasters with high-performance insulation may save up to 25% in energy. This thermal retention supports even roasting results and prevents abrupt temperature drops that require additional power.
Which Materials Are Most Effective for Roaster Insulation?
Mineral wool and ceramic fiber insulation are popular due to their high heat resistance and low thermal conductivity. Mineral wool offers durability and fire resistance, while ceramic fibers maintain excellent heat retention at high temperatures. Spray foam insulation and reflective radiant barriers may also be used, sometimes in combination, to further enhance energy retention.
How to Retrofit Existing Roasters With Improved Insulation?
Retrofitting involves conducting an energy audit to identify heat loss areas. Solutions include adding external insulation jackets, wrapping internal components with high-temperature materials, upgrading door seals, or replacing outdated panels with modern ceramic fiber blankets. Such upgrades typically achieve a 15%–20% reduction in overall energy use.
How to Calculate Roasting ROI Based on Energy Efficiency Improvements?
Calculating the ROI for energy efficiency improvements is key to justifying changes. By comparing cost savings from lower energy bills and reduced wear on components to the investment in new equipment or insulation, roasters can realize clear economic benefits.
What Costs Should Be Included in Roasting ROI Calculations?
Include the capital expense of new equipment or insulation, installation fees, and ongoing maintenance costs. Also factor in savings from lower power bills and reduced component wear, and monetize benefits like extended equipment lifespan and improved product quality.
How Does Reduced Power Consumption Impact Profit Margins?
Even a modest 10% reduction in power usage can lead to significant savings. Lower power consumption reduces one of the major operational costs and can allow roasters to reinvest savings or pass reduced costs to customers, enhancing competitiveness.
What Tools and Formulas Help Calculate Roasting ROI?
A basic ROI formula is: ROI (%) = [(Annual Energy Savings – Annual Maintenance Costs) / Total Investment Cost] × 100 Advanced data logging systems, digital energy audits, and simulation software provide precise measurements for more accurate ROI predictions. Many roasters see ROI gains within 12 to 18 months of implementing energy efficiency measures.
What Are Sustainable Roasting Practices That Enhance Energy Efficiency?
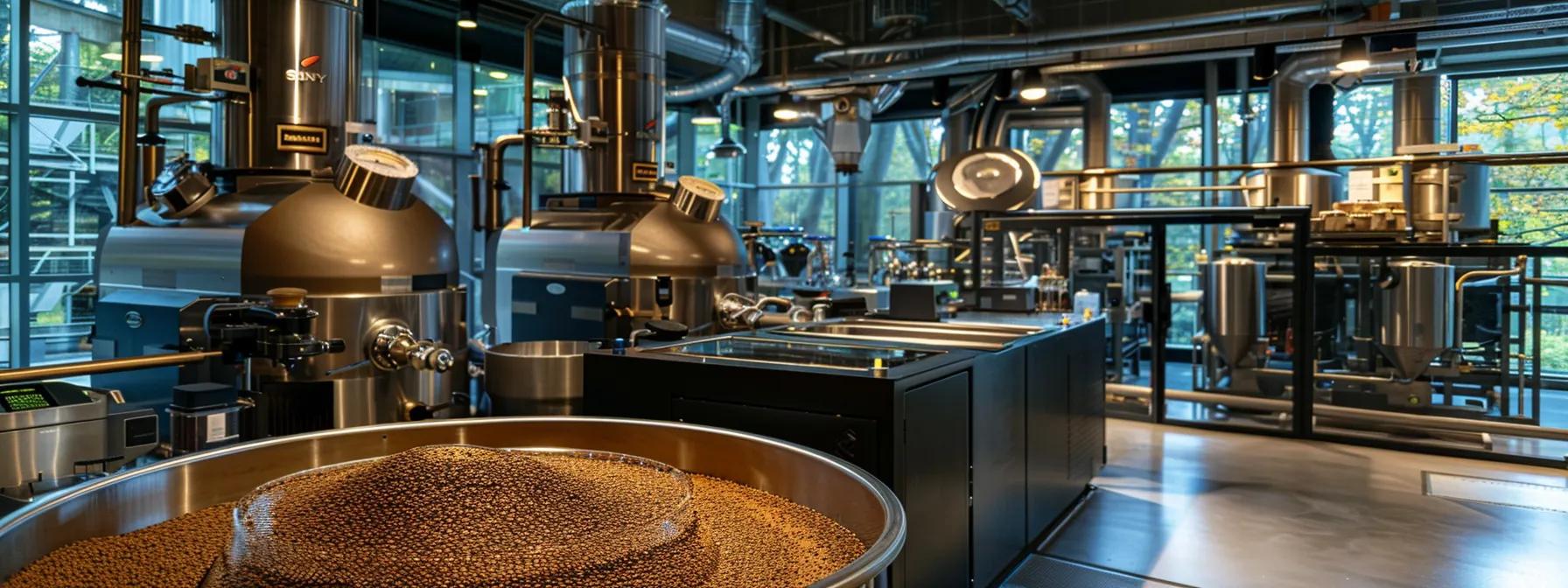
Sustainable practices reduce energy consumption, lower emissions, and use renewable resources. These practices are particularly important for specialty coffee operations that align with ecological values.
How Do Sustainable Practices Lower Environmental Impact?
Practices such as recovering and reusing waste heat decrease both energy consumption and emissions. In one operation, a heat recovery system reduced carbon emissions by over 18% and lowered energy bills. Using bio-based fuels or renewable energy sources further reduces the environmental footprint.
Which Energy-Efficient Technologies Support Sustainable Roasting?
Technologies like heat recovery systems capture waste heat for preheating, while automation and advanced control systems adjust temperature and airflow to optimize consumption. Renewable energy solutions, such as solar panels, can also supplement power needs and further reduce dependency on conventional energy sources.
How Can Roasters Balance Quality and Energy Savings?
It is essential to implement energy-saving measures that do not compromise roast consistency. Proper insulation, for example, ensures even bean development while using less power. Precise automation for roast profiling allows for fine-tuning that balances flavor quality with energy efficiency. Regular testing and calibration help maintain this balance.
How Can Energy Audits and Consulting Improve Roaster Efficiency and ROI?
Energy audits and consulting services help identify hidden inefficiencies. Expert consultants use tools like data loggers and thermal imaging cameras to analyze energy flows and recommend tailored improvements, leading to measurable savings.
What Is Included in a Coffee Roaster Energy Audit?
A comprehensive audit examines the heating system, airflow patterns, insulation performance, and overall operations. The audit report provides quantitative data on potential energy savings and highlights components needing upgrades, setting measurable ROI targets.
How Do Expert Consultants Identify Energy-Saving Opportunities?
Consultants compare current practices with industry benchmarks using software tools and hands-on expertise. For example, fine-tuning airflow during the cooling phase can reduce energy use by nearly 12% without affecting roast quality. Their actionable recommendations frequently lead to significant cost savings.
What Are the Typical ROI Gains From Professional Energy Efficiency Consulting?
Many roasters report ROI gains of 15%–30% within the first year after implementation. The initial audit cost is quickly offset by cumulative savings, with payback periods often under 18 months. Regular audits help maintain a culture of efficiency.
What Are the Latest Innovations in Energy-Efficient Coffee Roasting Equipment?
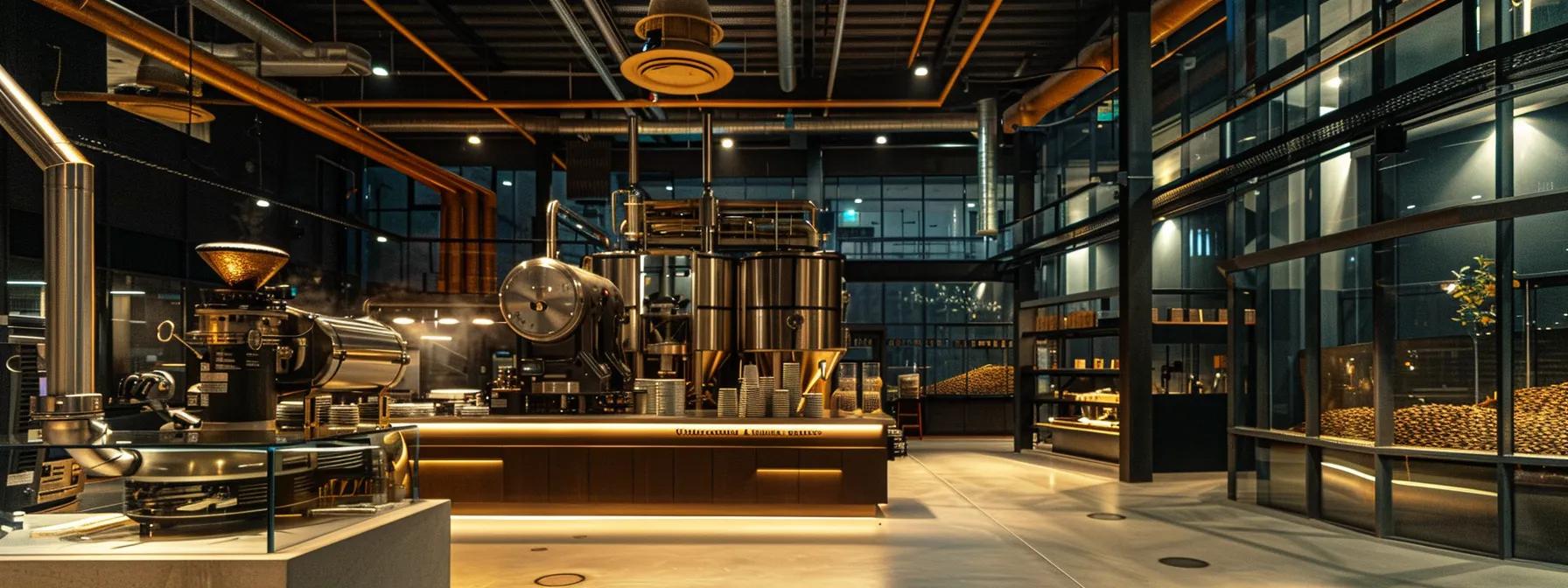
The coffee roasting industry is evolving through innovations that improve energy efficiency without sacrificing roast quality. Recent advancements are driven by improved heat transfer dynamics and real-time data monitoring.
How Do Heat Recovery Systems Reduce Roaster Power Consumption?
Heat recovery systems capture waste heat to preheat incoming air or support other heating needs, reducing the load on primary heating elements. Effective installations have shown energy consumption reductions of 15%–20%, while also enhancing roast consistency and stability.
What Role Does Automation Play in Energy Savings?
Automation systems use sensors and machine learning to continuously adjust temperature, airflow, and heat input. This real-time regulation prevents over-roasting and minimizes unnecessary power use. Modern roasters often incorporate integrated automation platforms that deliver consistent results and detailed energy consumption data.
Which New Roaster Models Offer the Best Energy Efficiency?
New models are engineered with enhanced insulation, integrated heat recovery, and sophisticated automation controls. Many of these models deliver up to 25% energy savings compared to older systems. Features to look for include real-time energy monitoring, custom roasting profiles, and connectivity options that provide detailed consumption analytics.
How to Maintain and Monitor Roaster Energy Efficiency Over Time?
Maintaining peak energy efficiency requires ongoing maintenance and regular monitoring. Even the best roasters can lose efficiency due to wear, residue buildup, or changes in operating conditions. Systematic maintenance and continuous energy monitoring are essential to preserving efficiency gains.
What Routine Maintenance Practices Support Energy Savings?
Regular tasks include cleaning the roasting chamber, calibrating temperature sensors, and inspecting insulation for degradation. Replacing worn seals and filters helps maintain optimal airflow and heat retention. A scheduled maintenance plan with visual inspections and performance tests prevents energy losses.
How Can Energy Consumption Be Monitored Effectively?
Digital energy meters and software-based data loggers provide real-time power usage data, enabling quick identification of fluctuations or inefficiencies. Integrating these systems with automated controls allows dynamic process adjustments. Routine audits and daily monitoring ensure any deviations from normal conditions are promptly addressed.
When Should Roasters Consider Upgrading for Better Efficiency?
Upgrades should be considered when maintenance costs rise or when older systems no longer deliver improved energy savings. Incremental improvements in insulation and automation can yield measurable gains. If energy metrics drift upward despite regular maintenance, it may be time to invest in newer, more efficient models—often every five to seven years.
Table: Comparison of Key Energy Efficiency Components in Coffee Roasters
Before the final considerations, the table below summarizes essential components, their functions, and impacts on energy conservation.
This table reinforces how strategic improvements can reduce operational costs and improve roast consistency.
Frequently Asked Questions
Q: How can I determine if my roaster’s insulation needs upgrading? A: Monitor heat loss during the roast and review energy consumption. Excessive power usage or inconsistent temperatures indicate it may be time for better insulation.
Q: What is the most effective material for retrofitting roaster insulation? A: Many roasters prefer ceramic fiber or mineral wool because of their excellent heat retention and durability under high temperatures.
Q: How quickly can I expect to see ROI improvements from energy efficiency upgrades? A: With proper monitoring and maintenance, many roasters notice ROI within 12 to 18 months after implementing improvements.
Q: Do automated control systems significantly affect energy efficiency? A: Yes, automated systems can reduce excess energy usage by up to 20% compared to manual controls by dynamically adjusting temperature and airflow.
Q: Can sustainable practices in coffee roasting reduce my overall environmental footprint? A: Absolutely. Techniques like heat recovery, renewable energy use, and precise process automation dramatically reduce carbon emissions and energy consumption.
Final Thoughts
Coffee roasting efficiency is vital for maintaining high-quality roast profiles while reducing operational costs and environmental impact. By focusing on power consumption factors, investing in proper insulation, and carefully calculating ROI, roasters can significantly improve their energy management. Regular energy audits and the latest innovations in automation and heat recovery ensure these gains are maintained over time. As the industry evolves, ongoing commitment to sustainable practices and technological upgrades will continue to pave the way for long-term success and profitability.
Let Coffee Crafters Help You Become A Coffee Roaster
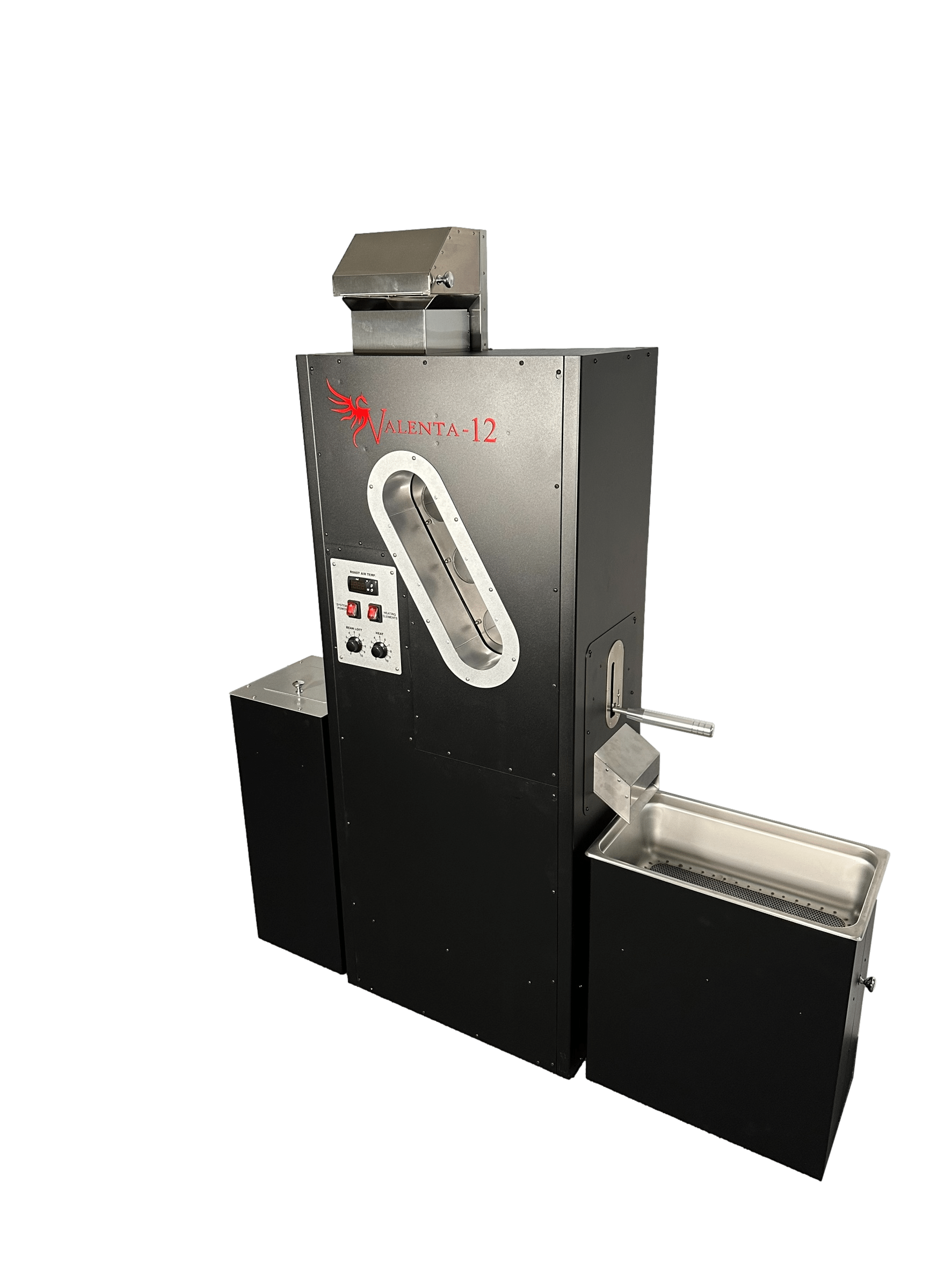